よもやま話
1. ダイヤモンド砥粒の話
ダイヤモンドは、この地球上では最も硬いとされている炭素の結晶体であるから、ラップ用の研磨砥粒として活用すれば、かなりなラップ効率が図れるだろうという「期待」が生じる。
事実、ほとんどの作業者は、ダイヤモンド砥粒の採用を試行し、あるいは、常用されていることだろうと予想されるわけである。
当然なことながら、私も利用を図ったことがある。
写真(上)は油性のもので、現在ではいろいろな供給元から市販されている。
砥粒が油で練り込まれているわけだが、この油の潤滑性能がハンド・ラップに際しては適性があるわけではなく、かなり使いづらいものとなる。
そのため、ハンド・ラップ用ではなくて、定盤上に塗布してワークをそこに押しつけるという、いわゆる「定盤ラップ」の場合に専ら使用している。
ハンド・ラップの場合には、やはり、写真(下)の砥粒自体を使用して、ハンド・ラップの用途に適した潤滑油(「ラップ油」)を独自に工夫するようにするとうまくいく。
砥粒そのものも、写真のように各社から市販されていて、それぞれ何がどう違うかという検証をしてみると面白い結果が出て来そうではあるのだが、天然ダイヤモンドか合成のものか、単結晶か多結晶か、分級の精度はどうか、といったいろいろな要素が絡んでくる問題ではある。
ダイヤモンド砥粒を使うという場合は、言うまでもなく、遊離砥粒ラップ/湿式というラップ技法になるわけなのだが、この技法でのラップ能力というのは「砥粒の自己破砕によって次々と新しい切り羽が自生してくるためにラップ能力が高い」と説明されている。
この説明は、確かに、WAとかGCの砥粒の場合をよく説明しているのだが、ダイヤモンド砥粒の場合に同じことが言えるかと考えてみると、当然のことながら「自己破砕性」というものは認められないため、ダイヤモンド砥粒それ自体の「硬さ」がラップ能力を決定しているということになるだろう。
つまり、ダイヤモンド砥粒を使う場合のラップというものは、第一次的には、硬いダイヤモンド砥粒粒子がワーク表面を滑走することによってワーク表面を光らせるというか、艶出しをする。第二次的には、ダイヤモンド砥粒の切り羽がワーク表面に刺さり込んで、そのままワーク表面を削ぎ取る。こういうメカニズムになっているだろうと想定できるところ、切り羽をワーク表面に「刺さり込ませる」ためにはかなりな加圧力を負荷しなければならず、ワーク表面を「削ぎ取る」ためには、その抵抗を押し切っていくだけの力を賦課しないといけない。
ハンド・ラップの場合、それだけの加圧力なり力を賦課するということはかなりな重作業になるため、結局は、ワーク表面を「艶出し」するに止まるということに終始する。
このような場合、ワークの下地処理で、例えば#6000~#10000で仕上げておけば、ダイヤモンド砥粒での「艶出し」はひどく容易で簡単なことになる。逆に言えば、#6000~#10000でワーク表面を仕上げることが出来ていれば、その場合の面粗度条件に基づけば、何もわざわざダイヤモンド砥粒で「磨く」「艶出し」をするということは全く必要性がなくなる。
つまり、結論づければ、例えばWA砥粒#3000以下の粗い砥粒で下地仕上げをしておいて、ダイヤモンド砥粒を使って鏡面仕上げをするという場合と、ダイヤモンド砥粒を使わずに、#6000~#10000で最終仕上げをやり切ってしまうことと、どちらが効率的で信頼性の高い仕上げ方法か、という選択の問題になる。
私自身の場合は、技術・技能のテーマの一つとしてダイヤモンド砥粒を使っての遊離砥粒ラップ/湿式という技法で、0.5μm砥粒を実務化したわけだったのだが、この場合の欠陥として、ブロックゲージを酷く損耗させる。超硬製保護ブロックゲージを使用するわけなのだが、超硬材というものは、その性質上、ダイヤモンド砥粒での湿式ラップに対しては損耗の度合いがひどく大きなものであるから、気休めにもならないことになる。
ダイヤモンド砥粒ラップの技法を放棄した所以である。
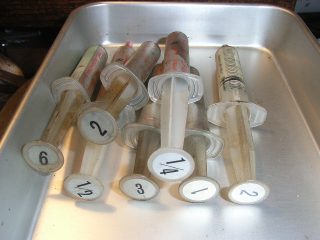
この「油」の実体は何かと問い合わせても、もちろん答えては貰えませんが、別売の「希釈駅」でその効用を調整するんだということでした。
定盤ラップの場合には、このままで使用しても上手くいくわけですが、ハンド・ラップの場合ではその油膜の膜面が硬すぎるということです。
2. 定盤ラップ用定盤
私らの日常的な仕事の範疇では、さまざまなものの面をラップするという仕事があります。
その際には、「定盤ラップ」という方法、即ち、平面が丁寧に仕立てられた定盤上にラップ砥粒を均一に塗布し、その上でワークを動作させてワークの当たり面をラップする、という技法を利用します。
通常は、ワーク材質が焼き入れ工具鋼(SK材)の場合、鋳物製の定盤にWA砥粒を用いてラップするという方法になりますが、この場合のラップ砥粒の粒度は#4000位が限度になります。鋳物製定盤で#6000WA砥粒を使うというのは、ほぼ無理なことになります。
ダイヤモンド砥粒を使う場合、鋳物製定盤では弊害が大きいので、右の写真のような燐青銅製の定盤を自作しました。
一般的には、銅製定盤にするとか、あるいは、ラップ盤用のラップ円盤として軟らかな金属を採用するということが試みられていますが、私の個人的な試みからいうと、これらの場合はダイヤモンド砥粒の「保持力」が弱いためあまり芳しい結果が出ません。燐青銅であると、この「保持力」が秀でていますから、0.5μmあるいはそれ以下の微細なダイヤモンド砥粒粒径のものに対しても有効な研磨力を発揮します。
つまり、一般に理解されているような、ダイヤモンド砥粒での「遊離砥粒ラップ/湿式」としてラップが行われるのではなく、実質的には「固定砥粒ラップ/乾式」によってラップが作動しているという理解がないといけないわけです。
使い方は、通例な定盤作りと同じで、
1.GC砥石等で平面を仕立てる。
2.アルカンサス砥石等で、ダイヤモンド砥粒+ラップ油で、定盤上に均等にラ ップ砥粒が分布するように押し込む。
この場合、定盤全体がごく僅かに凸面になるように仕立てられないと、ワー ク面を平面にラップ仕上げすることが出来ません。
よくある話として、定盤面が厳密に平面でないと、ワーク面を平面に仕立て 上げることが出来ないと教える向きもありますが、それは間違いです。
3.定盤上でワーク面を摺動させて、ラップ仕上げを行う。
定盤面の面性状が、仕立て上げられるべきワーク面にどのように影響するかを弁えて作業に当たることが、仕上げ品質を決定づけます。
従って、上に「GC砥石で平面を仕立てる」場合、その定盤が余りに柔弱な材質であれば、定盤としての面性状を維持していけませんから、定盤作りが極めて難しくなります。また、余り大きな定盤にしてしまうと、その定盤面の維持や手直しが大変な作業になってしまいますから、必要なだけの小さなものにしないといけない。写真のもので、80×105mmです。
右の写真のものは、焼き物を整形したものの一面を、ダイヤモンド砥粒とプラスチックを練り込んだものを塗布し固めたもので加工面としたものです。
一般市販品です。
見た通り、固定砥粒ラップ/乾式のものになります。
但し、精密なラップ作業にはちょっと力不足ではあります。
3. ダイヤモンド砥粒を使う場合の定盤
ゲージ屋の仕事として、ハサミゲージの製作に際してダイヤモンド砥粒を使う場合、砥粒を置く定盤と、ハンド・ラップを行うラップ工具との組み合わせが前提となる。
この場合の定盤の役割というのは、①ラップ油とラップ砥粒をよく混和してラップ工具の面上に均等にラップ砥粒が分布するようにすること、②ラップ砥粒を固定させて、ラップ工具表面をラップ砥粒がよく「引っ掻いて」ラップ工具表面のラップ滓を除却し、併せて、ラップ砥粒がラップ工具面上に確実に保持されるようにすること、という点にあるわけなのだが、この場合、ラップ工具表面というのはラップ方法として「固定砥粒ラップ」用の工具となっていることに注意しておこう。
右の写真は、よく使われていると思われる「ガラス定盤」。
ガラスを使った場合、定盤上でダイヤモンド砥粒がよく保持されず、固定されないため、従って、ラップ工具面上での面性状の維持の効用があまり芳しいものとは言えない。
これに対して、下の写真は石英の板。
石英版を利用すると、ダイヤモンド砥粒を保持・固定する力が強く従って、ラップ工具面上に対する面性状の維持の効果も大きい。
つまり、問題の所在は、ラップ工具面の面性状が、ハンド・ラップという作業においてどうあらねばならないかという観点から、定盤の物性が判断されないといけないのだが、その場合、ラップ工具の材質が必ずしも鋳物であることが必須条件になっているわけではない。
細かな議論は省略するのだが、鋳物をラップ工具とする場合、WA砥粒で#4000~#6000程度が上限となり、ダイヤモンド砥粒の場合はほぼ3μm粒径が上限となって、それ以上に微細な砥粒は使えない。定盤の側も同じことが言えるわけだから、ダイヤモンド砥粒で1μm粒径の者を採用して鏡面ラップを目指そうとするならば、鋳物という素材は全くの役立たずになる。
では、どのような素材が最も適切かということになるのだが、結論から言えば、ダイヤモンド砥粒がよく刺さり込んでそのまま固定され保持されるべき表面性状を有していること、という点に尽きる。
ガラスの場合は、ダイヤモンド砥粒が刺さり込みがたく、石英の場合は刺さり込んで固定されやすいが、内部的に脈があったりして素材としての均一性に欠け、容易に砕けやすい。加工もかなり厄介なことになる。
4. ラップ工具いろいろ
右の写真は、使用しているラップ工具のいろいろです。
「鋳物」を用いるということが一般的だと説明され、鋳物と言っても種類というのがさまざまにあって、そのうち「ネズミ鋳鋼」が最もラップ能力が高いとされています。しかしながら、なぜ「鋳物」かと言えば、その組織構成において微細な「穴」がありますから、その「穴」にラップ砥粒が嵌り込んでグリップされるということによります。ですから、同じ原理に立つ材質があれば、それはラップ工具として有効なものになるだろうという予測が立ちます。
「鋳物」の場合でのこの「穴」では、#3000程度の砥粒粒径で最も保持力が高く、上限としては概ね#6000程度になります。従って、#8000~#20000の砥粒を使おうとする場合は、この「穴」がその粒径に相当すべき微細なものでなければならず、そのような工具素材は、改めていうまでもなく、鋳物以外に数多存在しているわけです。
もちろん、この点はかなり以前から理解されていて、それぞれの作業者で工夫と創見が繰り返されてきましたから、何も改めて「私の創見である」などと主張できるものではありませんが、いろいろと幅広くテストを繰り返して、その知見に新たな経験を追加したという点はあるでしょう。
つまりは、必ずしも「鋳物」にはこだわらないという「構え」がないと、工具の改善なり性能評価はかなり無理が生じます。
ゲージの製作過程で、放電加工機でベースの加工を行い、後はその加工痕を消除すれば良いだけという製作工程であれば、ラップ・レベルということは余り意識されないかも知れません。
しかしながら、ゲージ測定部に対する機械加工は、その部分に応力集中が必ずもたらされているという考え方に立てば、その部分を丁寧に除却しておかないと寸法変位の原因になるわけですから、仕上げるべき寸法値のかなり手前から手作業であたらないといけません。
従って、0.01mmレベルでゲージ測定部を摺り下ろす工程、0.001mmレベルで摺り下ろすべき工程、最終的には、0.0002mmレベルでラップ仕上げを完結・完了させるべき工程・・・と、工程設計をどうするかはそれぞれの「事情」によりますが、全体を同じ同一のラップ工具で賄えるはずもないわけで、それぞれの状況に応じての「使い分け」が必要になります。
ゲージ製作において最も時間を要し手間を要し緊張を強いられるのがこの仕上げ工程ですから、適切なラップ能力を発揮するべき工具の開発は、最も合理化効果の大きなものとなることは言うまでもありません。
ラップという分野は、ラップ盤を使う「機械ラップ」が圧倒的な比重を占めていますから、ハンド・ラップという世界は、大量生産には不適なもので、改善・改良の余地のほとんどない伝承的な職人技で、しかもその修得には長年月を要する困難なものだという「決め込み」で語られることが多いのですが、だから、機械ラップでの到達水準をハンドラップの世界に如何に応用できるかという発想に傾いてきました。
しかしながら、ハンド・ラップにはハンド・ラップに独自な「ロジック」がありますから、その「ロジック」の解明ということは大切な意味があります。
金型屋さんの世界では「鏡面仕上げ」ということが普通に取り組まれているわけですから、ゲージ屋、もそれに遅れず並んで行かないといけないと思うわけです。
5. 遊離砥粒ラップ/湿式の問題点
大分以前の問題になりますが、焼き入れたダイス鋼について、WA砥粒#3000+鋳物製ラップ工具でラップ加工を試みたことがあります。
もちろん、ラップ能力が不足しますから、なかなか摺り下ろしが出来ないわけですが、ある程度の回数を繰り返していくうちに、ワークの表面に「ピンホール」が生じてきます。これを消除するためにいっそう力を込めてラップしようとすれば、この「ピンホール」の数がいっそうワーク表面に多く発生してきますから、とりとめのないことになります。
この原因が、実は、未だに分からない。
ワーク表面に対して、その金属組織上の何かを「剥ぎ取る」ようなことになっているわけですが、その何を剥ぎ取ることになっているかが分からない。
いずれにしろ、この方法では、ダイス鋼に対するラップ仕上げは出来ないという結果は明らかですから、この現象は「遊離砥粒ラップ/湿式」に特有な病理現象と結論づけました。
ダイヤモンド砥粒とかの他の砥粒を使えばどうなるかは、やってみる意味はあるかも知れませんが、自分ではやっていません。
ある研磨材のメーカーの方と話をした際に、「ダイス鋼のラップの場合にピンホールが出ませんか?」という指摘がされたものですから、かなり一般的に生じる現象のようです。
もう一つの経験は、超硬材に対するダイヤモンド砥粒ラップを試みた際の問題。
超硬材と一言で言っても、いろいろとバリエーションがあって、自分が試みた超硬材がどのようなものであったか具体的にその種類を特定することは出来ませんが。
1μm粒径のダイヤモンド砥粒を使っての湿式ラップに際して、そのワーク表面をボロボロと崩していくわけです。つまり、超硬材というのは焼結材ですから、超硬粒子を結合させている結合材に対してダイヤモンド砥粒が作用してワーク表面を突き崩していくわけです。
超硬粒子は、言うまでもなく極めて硬いものですが、結合材はそれに比較すれば極めて柔弱なものですから、どんどんと超硬粒子をばらけさせていきます。
1μm粒径のダイヤモンド砥粒でワーク表面を突き崩して、次に、1μm以上の大きな粒径のもの、もしくは、例えば0.5μm粒径といった微細な粒径のものを使えば、超硬粒子に対してラップしていくことになりますから、綺麗な鏡面になっていくわけです。
この技法を巧く使えば、超硬部分の仕上げ代が多少大きなものであっても、かなり簡単に寸法仕上げが可能になるということを意味します。
現状では、ダイヤモンド砥粒を使ってのラップ作業では、3μm粒径が限界であるとか、2μm粒径を使っているとかの話はよく聞きますが、0.5μmないし1μm粒径を使いこなせるようにすれば、超硬材のラップ加工というのはかなり容易なものとなるだろうと思えます。
同じことは、セラミック製ゲージに対するラップ加工でも言えるわけです。
固定砥粒ラップではこういう操作は不可能です。
超硬材ないしセラミックスに対するラップ加工の場合は、遊離砥粒ラップ/湿式という技法が極めて有効な作業となります。
6. cBN砥粒
右の写真はcBN砥粒。
購入単位は、ダイヤモンド砥粒の場合と同じような条件で、50ct.あるいは100ct.単位での購入になる。
大体がcBN研磨材(例えば、丸砥石)の製造原料として販売されているものだから、ごく僅かな量を売って欲しいと言うと、一呼吸待たされる。
ラップ砥粒としての用途を言ったのは、多分、客としては私が初めてのことだったらしい。
分級のレベルとしては、ダイヤモンド砥粒に比べて、やや幅広いものが多いが、限定すれば精度の良いものが入手できるかも知れない。
使い勝手は、ダイヤモンド砥粒とほぼ同じで、ダイヤモンド砥粒を巧く使いこなせる道具立てでcBN砥粒も活用できる。
使ったときの感覚は、「硬質GC」とでも言うべきか、GCの劈開性がないものというところではある。
7. 砥石ラップという技法
現在、私が採用しているハンドラップ技法は砥石ラップというものなのだが、これは全くの私の創見になるものではなくて、3・4年前の読んだある専門書で、著者の大学研究者(教授)が開発されたもので、その原理とオペレーションについて説明されていたわけだった。
もっとも、おそらくは特許でガチガチに固められているものと思えるのだが、通常ならもう少し詳細な論述があって然るべきはず(何せ「教科書」なんだから)なのだが、悪く言えば「仄めかしている」ような記述ではあった。
当時は、湿式/ダイヤモンド砥粒0.5μmラップの技術・技能が開発できていて、これで鏡面ラップ仕上げの技術・技法は完璧と自得していたのだが、やればやるだけ、その「弱点」というか、解決できない問題点も自覚できるようになっていたから、その突破口というか、改善の方向に迷っていたわけだった。
つまり、どういうことかというと、ダイヤモンド砥粒でのラップというのは、最終的な仕上げラップであって、仕上げるべき寸法で鏡面仕上げをする直前までは、別なラップ方法で作業を進めている。この作業のまま、鏡面仕上げで寸法を実現できれば、何もダイヤモンド砥粒での仕上げラップをするまでもない。ダイヤモンド砥粒ラップという方法が、必須・不可欠な工程であるかどうかと考え直してみれば、別な、もっと効率の良い方法があれば、別に放棄しても構わないものになるだろう。
砥石ラップという方法が採用されるということは、砥石ラップというのは乾式ラップの原理になるから、ハサミゲージ製作の歴史を根底的に転倒させるものとなるだろう。
そんなことが果たして可能かという不安が常につきまとうことになった。
「この砥石をもってくれば、自在に砥石ラップをすることができます」というわけではなくて、道具というものは、それを行使するためにはさまざまな条件というものが不可欠で、その条件をどう確定していくかに膨大な時間(手間)がかかる。
研磨材屋さんにも、よく機会を捉えては、いろいろと聞き合わせもしたりしたのだが、やはり、自分の使用条件というのは自分で確定していく以外にはないわけだ。
ほぼ3年がかりで開発は終わって、現在ではその方法のみで全部の作業を賄っているのだが、現在の私のやっていることが道具総体の最適条件を満たしているかどうかは分からない。道具が具備している効能が最大限に引き出せているかどうかは、計測できないから、もっと別な条件を実現できれば、いっそうの効率化が図れるのかも知れない。
つまり、最適条件が実現できているか否かは、ひたすら「数をこなす」ことで考えていかないといけない。
だから、なかなか確信が持てないわけだ。
ただ、目的に向かってひたすら一直線というわけではなく、いろいろな道具を考えて試用してきて、目的に対しては「削ぎ落とした」ものが幾つかある。目的には適合しない、あるいは、効率が悪いと判断して放棄したものの内に、もっと目的に適合的なものがあったかも知れない。それがどうかは、今更ながら、もう一度開発過程をお復習い(おさらい)するわけにもいかない。
だから、私のやっていることが、唯一無二なものと主張することはできないわけなので、もっと「集合知」というものの実現に期待する以外にはないわけである。
なお、砥石ラップという原理は、簡単明快なものだから、機械ラップの世界では旧くから試みられてきた技法である。
ただ、問題点があって、それは、砥石面の「目詰まり」をどう解決して、砥石のラップ効能を如何に安定的に持続できるかが、技術的な課題となる。
ごく乱暴な解決策として、砥石表面に固着したラップ滓を「溶解してしまう」というのがあるのだが、なかなか安定的なものにはならないから、依然として湿式/遊離砥粒ラップがメインとなっている。
ところが、ハンドラップの世界では、砥石表面のラップ滓は払拭すれば良いだけというわけだから、まるっきり問題とはならない。だから、乾式/固定砥粒ラップという技法が、ハンドラップの技術的・技能的特質として、機械ラップの世界と画然と区別するものとなるだろうと、私は考えているわけだ。
ついでに言っておくべきことかも知れないが、教科書等には、「ラップには、遊離砥粒ラップ/湿式と、固定砥粒ラップ/乾式の、二つの方法」があると、並列的に説明されているのだが、こういう説明だと、ここで止まってしまうわけなので、正しくは、「ラップというのは、固定砥粒に基づく加工工程で、それには湿式と乾式とが区別される」としないといけない。
学者というのは面白い議論の仕方をされるようで、「「乾式」と言っても、油/水を使っているだろうが」、と。
つまり、湿式というのがラップに通底している「原理」だとされるわけなのだが、ラップに使用されている油/水というものの役割・効用が、この二つの方式の区分けの下では違っているわけなのだ。その違いを指摘できて初めて成り立つ議論ではないのかと、考えている。
通例、ラップ工程で使用されるラップ油(水)を、砥粒を均等分散させるための「キャリアー」だとする位置づけで説明されるわけなのだが、それで説明が尽きてしまうなら、それで必要十分なことであるなら、私は今までこんな苦労はしてこなくて済んだわけだ。
8. ブロックゲージとリンギング
ゲージ屋がその技術・技能の目標とするのは、「ブロックゲージ並みの面粗度・平面度・平行度・寸法」なのですが、そのうち、先ずは、そのラップの面粗度と平面度が目標となります。
具体的に言えば、任意のブロックゲージの面ときちんとリンギングするようなラップ面を仕立て上げられるようにするにはどうしたら良いかということがテーマになるわけです。
2個のワークを作成して、それぞれの端面を仕立て上げています。
リンギングの生じる条件というものがあります。
例えば、#3000で仕立て上げてもリンギングは生じなくて、#6000程度からリンギングの現象が現れる。
0.1μmのオプチカル・フラットで検証する平面度で、光筋3本程度でもリンギングが認められる。
細かく検証していけば、そこには何か法則的な「関数関係」が認められるでしょうが、そういうことの検証に際しては、ハンド・ラップの技術・技能を適用する以外には困難だと思えます。
ラップをした場合、必ず「ラップ痕」というものがワーク表面に刻まれます。従って、いかなるラップ痕も完全に消去されていなければ「鏡面」とは言えないと、硬く主張される向きもあるのですが、なかなか難しい話になります。
なぜならば、遊離砥粒ラップ/湿式で、0.5μmのダイヤモンド砥粒を使ってラップした場合、ワーク表面に刻まれる凹凸の高低差は10nm以下のものになるわけですが、しかしながら、この高低差をラップ痕として、人間の視力は視認するわけです。
従って、ハンド・ラップでのラップという作業ではラップ痕を完全に消去することは出来ないと割り切って、それ以上のことについては、「もう一味別な工程」を要すると考える必要があるのかも知れません。
機械ラップの世界では、ラップ工程に引き続いて「ポリッシュ工程」が設けられていて、その工程段階でラップ痕を消除するというようにされているわけですが、ハンド・ラップの世界で、そのような「ポリッシュ工程」が設定されなければならないかは、別に議論の必要があります。
この写真のサンプル例の説明をしておく必要があります。
ワーク材質はSK3。8Tのもの。
この材料は、焼き入れ硬度でHRc64が出ます。
ラップ方法は、#8000。
#10000ないし#30000といった超微細なラップ材でないと鏡面は仕立てられないとか、リンギングを実現できないとは、全く考えていません。いろいろな条件絡みの話にはなりますが、#6000でラップ痕を消除できた「鏡面」を仕立て上げることが可能です(但し、固定砥粒ラップ/乾式の場合です)。
最後に、なぜ「鏡面」かという話(疑問)になってしまうわけですが、ワーク表面の面粗度が微細になるに従って、そのワークそれ本来の物性が良く引き出されて、その耐摩耗性が最大限に発揮されるわけです。
同時に、ブロックゲージの寸法精度条件をワークの側に精確に引き写せるわけですから、高精度なゲージ寸法値を容易に実現することが出来るわけです。
9. 鏡面ラップの技法
ゲージの製作に際しては、目標とする寸法値が仕上がる時点で、その測定面が鏡面に仕上がっているという状態を目指すものですから、寸法を追い込む(摺り下ろす)という作業と鏡面に仕立て上げるという方法とが、言わば「連続性」を持っていないとはなはだ作業性が悪い。効率が悪いわけです。
従って、機械ラップの世界でのように、ラップ工程とポリッシュ工程を画然と区分するという方法は、ゲージ屋のハンド・ラップの世界では採用できるものではないわけで、ラップ工程=ポリッシュ工程という具合に、最終段階ではならないといけない。
従前、ゲージ屋は「鏡面仕上げ」ということを意識して、どのようにしてきたかというと、例えば、一つには、「空ラップ」という方法があります。最終的に、ラップ工具表面に付着してきたラップ砥粒を完全に払拭して、ラップ工具表面(鋳物)とワーク表面(焼き入れたSK材)とを直接に摺り合わせるわけです。両者間にさほどの硬度差がなければ、両面の高いところがそれぞれ相互に潰されていき、それなりには「艶出し」が出来るという方法です。二つには、よくある話ですが、「酸化クロム」を使ってラップするという方法です。いわゆる「磨きの工程」になるのですが、ラップ工具表面の物性に比べて酸化クロムは適切なものとは言い難いので、結構難しい作業になります。
ラップ加工でラップ砥粒を使うわけで、ラップという動作で必ずラップ痕がワーク表面に刻み込まれるわけですから、そのラップ痕をどう消除するか。原理的には、どんな微細な砥粒を採用したとしても、そのラップ痕は消除できないという結論になりそうです。もっとも、そのラップ痕の幅と深さがどれ位であれば「鏡面」として視認されるかは既に研究されて結論が出ていますから、それに相当する粒度でラップ加工をすれば、ごく当然に鏡面に仕上がるというわけです。
実務的には、例えば、0.1μm粒径のダイヤモンド砥粒でラップすればそれで決着してしまうわけですが、そういった結論に帰着させる前に、ゲージ製作者としてはもう少し考えなければならないことがあるだろうと思うわけです。
遊離砥粒ラップ/湿式の場合、ラップ工具表面にあるラップ砥粒の切り羽が一つの面上に揃うというわけではなく、ランダムに動きますから、必ずラップ痕が生じます。また、だからこそ、この技法でのラップ能力が高いわけです。
この場合、砥粒の切り羽の先端を一つの平面上に「揃える」ためにどうすればいいか?
精度の良い(適切な平面度を具備している)ラップ工具表面に、ラップ砥粒が濃密かつ均等に分布していて、それに対してラップ工具に加圧力を負荷して、ワーク表面に均一な力でラップ砥粒が押しつけられる。
こういうロジックで、ワーク表面が均等にラップされ、ラップ痕がそれぞれのラップ砥粒の働きで潰し合いがなされる。
0.5ないし1μm粒径のダイヤモンド砥粒を採用する場合、こういうことで「鏡面」が仕立て上げられるわけです。
通常よく説明されていることは、ラップ痕そのものの幅や深さを極小にするために、出来るだけ加圧力を小さく軽減させ(軟らかなラップ工具を使う)、かつ、ラップ痕をそれぞれ潰すためにはラップ工具を高速で動作させる(ラップ砥粒がワーク表面に接触する回数をいっそう増やす)、ということが紹介されますが、ここでは、それとは「真逆」な方法を指摘します。
遊離砥粒ラップ/湿式の方法で、ラップ砥粒の切り羽の先端を揃えるということは、つまりは、遊離砥粒ラップの方法で固定砥ラップを行うということを意味します。
そうであるならば、最初から固定砥粒ラップの方法を採用すれば、それ程も神経を使わずに済みますし、加圧力をいっそう大きく負荷するという「重作業」にならなくて済みます。従来から、固定砥粒ラップの方法の方が鏡面仕立てが容易であることは指摘されてきたことではあります。
固定砥粒ラップの場合、砥粒間の「距離」というものが固定されてしまっていますから、その砥粒間の離間距離が大きいとラップ痕が必ず生じるということになります。固定砥粒の固定方法で必ず弾性がありますから、この弾性による砥粒の切り込みが無視できないわけです。
従って、固定砥粒ラップの場合、その固定砥粒のラップ力でラップを行えば、その粒度に応じたラップ痕が生じるわけですが、それと同時に、ラップ工具表面にはワークをラップした後のラップ滓が蓄積されていきます。このラップ滓が、砥粒間の離間距離を埋めていくわけです。注意されるべきは、この段階で、ワーク表面とラップ工具表面上のラップ滓が、つまりこの両者は同じ物性を持っているものですから、表面を潰し合いするわけです。砥粒は切り込み力がありませんから、ラップ痕は生じないわけです。
固定砥粒ラップの場合、このラップ滓の蓄積を如何に除却するかが大問題となっているようです。
しかしながら、こういった「目詰まり状態」が、ハンド・ラップの場合は、鏡面仕立てのポイントになります。
10. SUS420J2製ハサミゲージ
SUS420J2製ゲージを商品化できたのは1997年からのことですから、もう10年以上になっています。
「防錆」という問題の解決が必須な事情がありました。
それ以前には、ゲージ全体をクロムメッキを施して、ゲージ測定面のメッキ層は除却して仕立て上げるという方法を専らにしてきていたのですが、ゲージのごく一部の防錆措置もなかなか煩瑣なことになるらしく、ともすれば発錆を招いていたわけでした。
もう一つの方法として、ゲージ全体に硬質クロムメッキを施して、その硬質クロムメッキ層の厚さの範囲内でゲージ寸法を仕立てるという方法も採用しましたが、その仕上げ余地を大きく取ろうとすれば、メッキ厚み自体が全体では不均等なものですから、なかなか精確な仕上げ寸法とはなり難い。メッキ前に、そのメッキ層の厚みを勘案して一旦仕上げ、メッキ後にはまた最終的な仕上げをするという、言わば「二度手間」が掛かりますから、高コストにならざるを得ません。
それで、結局は、単純に焼き入れ可能なステンレス鋼が採用できれば、問題は解決してしまうわけです。
もっとも、ステンレス鋼を採用すれば単純に問題が総て解決するというわけではなかったわけです。
防錆の問題としては。
鉄鋼材料の発錆には、そのカーボン成分が大きく作用するわけですが、ステンレス鋼の場合、焼き入れを可能とするためにはカーボンを含ませる必要があり、カーボンが含まれれば発錆原因を抱え込むことになるという、二律背反的なことになります。
従って、カーボン分を含まないSUS304とかの材料に比べて、SUS420J2では「絶対に錆びないか?」と言えば「錆びないとは言い切れない」という結論になります。
しかしながら、ステンレス鋼の防錆能力というのは、煎じ詰めれば、材料表面の酸化クロム層が如何に適切に形成されるか、に集約されますから、その旨を込めた製作手順が確定できれば良いということになります。この点について選択すべき措置方法は幾つかありますから、ゲージの使用に際してさほど神経質になる必要もないわけです。
よく言っていることは、「SUS420J2もしくはそれに準拠したステンレス製品である『ノギス』が錆びますか?」ということです。測定機器類・工具類には、既に広く採用されている素材であるわけです。
どうしても錆一つ発生してはならないということであれば、SUS420J2製ゲージ全体に硬質クロムメッキを施すという方法(ゲージ測定面はメッキ層が除却されて、SUS420J2というベース面が露出するということですが)が採れるわけですが、メッキをしなくても、ベースの酸化クロム層は十分強度を保ち得るわけです。
材料強度の問題。
よく心配されることは、ステンレス鋼は柔弱な素材だから、ちょっと乱暴に扱われた場合、よく変形する(寸法変位をきたす)のではないか、という点です。
世間では、SK材製のハサミゲージででも「総焼き入れ」でないといけないとされるケースもよくあるようですが、そこで憂慮される原因・理由については、私は疑問を抱いてきているのですが、その点はともかくとして、材料強度の点に限って言えば、ナマ材か焼き入れ材かという二者択一の考え方には立っていません。ナマ材から焼き入れ硬化に至るまでの「中間段階」があるだろうと言うわけです。
総焼き入れをしてしまうと、例えば焼き入れの際に「曲がり」や「反り」が生じた場合、平面研削で是正できる程度ならともかく、そうでなければ、ガソリン・バーナー等で焼き戻しをかけて、その「曲がり」や「反り」を直すということがされてきましたし、あるいは、プレスで強引的に直すという手法も採られています。焼き入れたものはもう狂わないというのではなくて、ナマ材であろうと焼き入れ材であろうと、内部応力を原因とする寸法変位は避けられないことになりますから、こういった是正方法は、わざわざ寸法変位の原因を付加しているようなことになりかねません。
当方の材料強化の措置方法で、特に問題は生じて来てはいません。
なお、この点については、鉄鋼材料学や熱処理の教科書等で論及されている問題で、何も「経験」と「勘」によるものではありません。
以上の2点を特に踏まえて、ゲージの仕様条件が決まります。
SUS420J2の素材は、圧延の関係で、幅300mmが限度ですので、その範囲内で作れる形状のものはステンレス対応が可能となります。
SUS420製ゲージの仕上げ方法については、別の機会に説明します。
11. ハサミゲージの素材
ハサミゲージの素材については、JIS B 7420 -1997 では、「SK4もしくはそれ以上」とされ、焼き入れ硬度は「HRc60(以上)」と規定されている。
SK4というのはJIS鋼種名であるのだが、伝統的には、日立金属(株)が製造するYG4が採用されてきていた。なぜかと言えば、一般的な市販品で購入しやすいという点もあったが、主要には、「球状化焼き鈍し」が製鋼段階で徹底されていたため、工具鋼としての信頼性がいっそう高いものという評価があったからで、当然のことながら、焼き入れに際しても、余程のヘマをしない限りはHRc60は保証される材料なのであった。
ところが、経過的に言えば、このYG4がYCS3(SK3)に鋼種統合されて製造中止となり、程なく、このYCS3(SK3)に加えてSGT(SKS3)といった工具鋼からの生産撤退が実行され、日立金属(株)から供給される工具鋼というのはSLD(SKD11)といったダイス鋼類に製造が集約されることに至っている(薄板材に限っての話で、丸材に関しては、SK3/SKS3は引き続き製造されているらしい)。
もちろん、ゲージ屋段階でも素材のストックは有しているから、製鋼段階で製造中止となっても、直ちに材料に困るということにはならないのだが、しかしながら流通段階での在庫は既に払底しているから、いずれは、SK5製ゲージか・ダイス鋼製ゲージか、という時代に移行する。
当方では、問屋さんのご厚意でSK3/SKS3に関しては向こう10年分程のストックを有していて、別段素材調達に不安をきたしているわけでは全く無く、3種の素材を採用してユーザーの求めに応じている。
1.SK3/SKS3 一般JIS規格型ゲージ用
2.SUS420J2 特定ユーザー用途向け特殊仕様品用
3.SKD11 特定ユーザー向け
なお、焼き入れ可能なステンレス鋼には、SUS420J2以外に、SUS440Cがある。
SUS440Cは、検討当時では、4~6mm厚の板材が一般的にはないということ、薄板が必要な場合は「鍛造」で対応するという話であったため断念した経過がある。
そうこうしているうちにSKD11製ゲージが製作できるようになったため、SUS440C製ゲージでないといけないという事情は意味を失った。
SUS440Cは15%クロムであるのだが、クロム含有比率を高めた分だけカーボンの含有率を高めることが出来、結果として焼き入れ硬度を高くできるわけである。
これに対して、SKD11は12%クロム鋼で、1.5%カーボンにプラスしてバナジウムを加えている。ステンレス鋼に比べて「錆びないか」と問われれば「錆びることがある」と答えないといけないのだが、そう簡単に錆びるわけはない。金型等で広く採用されている素材だから、どういう物性を持った素材であるかはよく知られているわけである。
さて、ちょっと話は変わるのだが。
最近の情況として、例えば、高速度鋼(ハイス)製のゲージはどうかという照会があったりする。
ハイスの焼き入れ硬度としてHRc67があったりして、高硬度=高耐摩耗性という等式が念頭にある場合、いかにも採用すべき素材であるようにも思い込める。
被検証物であるワーク材質が何かという点との相関でゲージ材質が考慮されるべきなのだが、あるいは、ワークの表面粗度との関係でゲージの摩耗の情況というのが決まる面があるので、その点の考慮がどうかという問題があるのだが、その相関に思慮を欠くとゲージが刃物になりかねないということがある。
そういった基本的な条件ということは差し置いてハイス製ゲージを考える場合、焼き入れが非常に難しいわけである。最初に1200~1300℃に加熱しても十分な硬度は出ないわけで、その後に「焼き戻し」をして、その焼き戻しによってハイス鋼の本来発揮すべき焼き入れ硬度が出るわけだから、この焼き戻しの温度その他の条件をクリアできるか否かがポイントになる。
この点で言えば、フレーム焼き入れによるゲージ測定部への局部焼き入れというのが困難で、焼き入れ装置による総焼き入れにならざるを得ない。
焼き入れは何とかクリアしても、クリアできても、ハンドラップ仕上げはほとんど不可能だから、あまり精度条件の良好なゲージには仕立て上げられないだろうと想像はしている。
ハイス製ゲージを製作できると言い切っているメーカーさんがあるわけだから、技術・技能条件を克服されていることなんだろうとは思う。
超硬製のハサミゲージというのがよく宣伝されていて、当方でも検討したことはある。
「出来ない」という結論に至った理由というのは、以下のようである。
1.仕上げ代だけを残して(つまり、ナマな母材でゲージ形状を製作し、ゲージ測定部分に超硬製チップを貼り付けたもの)当方に供給するというメーカーさんがあったのだが、理屈の上では母材はナマ材であっては意味がなく、総焼き入れ材でなければならないのだが、その場合の、ゲージ屋に必須な経年変化対策だとかその他諸々の配慮要因を当該メーカーが履践するかどうかが分からない。
具体的に言えば、放電加工機による母材加工や、平面研削盤での平面研削で無理な負荷を掛けるようなことがあれば、品質保証が仕切れない。
2.仕上げはハンドラップになるが、ダイヤモンド砥粒での遊離砥粒/湿式では、ブロックゲージその他へのダメージが多きい。コストが大きなものとなる。
3.それだけの品質管理を行い、高コストな仕上げ方法を確立したとしても、超硬製ゲージを求めるユーザーというのは極めて限定されたものだから、言い換えれば、超硬製ゲージでなければ業務に差し支えるという特別・特種な用途であるはずだから、コストを見合うだけの需要はないだろうと想定できる。
通例、私のようなところに超硬製ゲージの照会があるというのは、超硬製ゲージを日常常務として製作しているメーカーさんの見積価格に不満があって、もっと廉価に製作できるメーカーがあるだろうという見込みなり期待を込めて、メーカーを探しているという事情なのだろうが、既に手掛けているメーカーさんと比較すれば、当方のようなところではむしろいっそう高コストになるという結論にしかならないし、あるいは、異例な特注では対応できないという話にはなる。
12. 特殊型外径用C型ハサミゲージ
「特殊型」というのは、一般的なJIS規格形状に対して特殊という意味で、顧客にとっては、これが「一般的」「標準的」な形状仕様であるわけです。
とかく、JIS規格形状を遵守しないといけないとか、JIS規格形状に拠っていれば無難だとかの考え方にこだわりを見せる向きもありますが、JISの規定それ自体で、この「規格形状」は参考例であって、他の仕様形状を排除・否定するものではないとされていますから、顧客の要望なり必要に従ってゲージ形状が決められて然るべきものです。
何が問題になるかというと、測定部長さがまず考慮されるべきことになります。
JIS仕様形状に拠る限りは、止まり部長さが短い(短すぎる)という点がまずあるのですが、ワークの規格によっては、JIS仕様形状での通り部長さでは、ワーク検定時に「ゲージの通り部がワーク計の頂点を超えない」ものとなります。
その辺りはどうなるかは事前に計算で検証しておくわけですが、ワーク計の頂点を超えるとしても、実際にゲージ通り部が通り部として有効に機能する長さがどうなっているかは、明確にされないといけないわけです。
次に、ゲージの「重量」の問題があります。
出来るだけ、堅牢で、かつ、軽量なものの方が作業性は良くなりますから、メーカーとしてはきちんと配慮するべきものです。
右の写真のものは、SUS420J2製です。
現場での寸法検証業務において、ゲージが錆びないということは大きなメリットです。一旦発錆してしまえば、ゲージの寸法精度は定義されるものとはなりません。
ステンレス鋼の場合、全く発錆から免れるとまでは言い切れませんが、SK材での発錆(いわゆる「赤錆」)が海綿状に体積膨張をきたすのに対して、ステンレス鋼の場合、錆の浸食情況はさほど大きなものとはなりませんから、ゲージの寸法精度の維持ないし寸法修復が容易なものとなります。
13. ラップサンプル:SUS420J2
材質 :SUS420J2 測定部焼き入れ(HRc56) 6t。
ラップ方法:固定砥粒ラップ/乾式 #10000
固定砥粒ラップの場合、どうしてもラップ痕が残ります。
材質それ自体の「硬さ」の問題はもちろんありますが、それ以外にも、表面情況というものが関わってきます。
つまり、ステンレス鋼の場合には、酸化クロム層がコーティングされたような状態になっていますから、その酸化クロム層を超えて砥粒が切り込めないとラップ加工ができないわけですが、完全な意味での鏡面にしようとすれば、そのベース部分と同時に酸化クロム層をどうするかという技能問題に突き当たります。
同じ情況はダイス鋼でも見られるわけで、試したことはありませんが、いわゆるSUJ鋼に関しても同様のことが語られ得ると考えています。
従って、#10000を超える微細ラップになると、この酸化クロム層と直接に向き合いことになりますから、ラップ動作を何回繰り返しても、ほとんど寸法に切り込めていないということが起こります。
この点が、ステンレス鋼(大きくいえばクロム鋼)での耐摩耗性の正体になります。
ベース部分が丸ごと鉄+カーボン+クロムの合金ですから、それだけでも粘り硬い材質なのですが。
酸化クロム層が厄介なのは、普通、ゲージ屋なら、酸化クロム粉末(いわゆる「青粉)で最終磨きを試みるということは一度は経験してきているわけなのですが、湿式では上手くいかないことは体感されていることだと思います。
14. 「鏡面」いろいろ
ハサミゲージ製作の場合、鏡面に仕立て上げるべきはワークの「内側」ですから、どうしてもハンドラップの技術・技法でどうすべきかという話に収束されてしまいます。しかし、ワークの「外側」について鏡面にすべし、という話であれば、別にハンドラップでなければならないという話に限定されるわけではない。
写真のものは、そういう用途に開発・販売されているもので、#2500相当程度のダイヤモンド砥粒を練り込んだラップ工具を使ってラップしたものです。
いわゆる「定盤ラップ」の技法に拠りますが、遊離砥粒ラップ/湿式ではなくて、固定砥粒ラップ/乾式になります。
もちろん、このレベルだとラップ痕は残りますが、強引に「鏡面だ」と言い張れば、「鏡面と認めましょう」という話になるかも知れない。
中途半端に「研磨シート」を使うよりは、仕上がり面の面性状は良好なものになりますし、何よりも、ラップ効率が良い。
以前お付き合いのあったフライス屋さんで、フライス加工の後、その切削痕を消去して欲しいと顧客から要求されたそうです。
平面研削盤で研削すれば済む程度の話だったはずですが、設備を準備していなければ人力でやる以外にはない。#240~#400程度のWA砥石で面を摺れば解決できるはずなのですが、(ゲージ屋の世界でも、#600程度のWA砥石で研削痕を消除してあればそれでOKというものは多いです)、残念なことに、その砥石をハンドリングする技術・技能がない。
研磨材屋さんに教えを請うと、いわゆる「不織布」を売りつけられたそうで、手間ばかり掛かって、その割には、「縁ダレ」が生じて役に立たないと嘆いておられました。
研磨材屋さんにしても、その用途・目的が奈辺にあるか、本人の技術・技能の水準がどうか、何を経験してきたか、で相談に対する回答が大きく異なってくるはずなのですが、その問題の立て方が的を射てないと「生煮えな話」に終始してしまいます。
鏡面にまで至らなくても、切削痕を消去する、研削痕を消除するという顧客要求は大きく拡がっていくだろうと思います。
今まで「ナマ材」の加工で良かったものが、焼き入れ処理したものが求められ、その「黒皮」の除却に際して「研磨加工」が求められるという筋書きです。
アルミ材の加工で、切削痕を消せと言われたという話は、よく聞きました。
ラップ盤が、大きなものから卓上の小さなものまで多種多様に開発され販売されてきている昨今ですが、量産品でない場合、あるいは、ラップ盤には載せ難い形状のものである場合、どうしても「手業」で対処できるように技術・技能が準備されていないと、具合が悪い。
機械ラップを掛けた場合、スクラッチが生じてワークをぶち壊してしまった場合なんかでは、その是正は手作業に拠らなければならないはずです。
私なんかでも、いろいろなレベルでの「磨き」「ラップ」を試みてきています。
15. 工作用と検査用
ゲージには「工作用」と「検査用」の区別があります。
本来の使い方としては、「工作用」ゲージでワークの加工をコントロールし、出来上がったワークについて、「検査用」ゲージで検定して合格品であることを確認して出荷に至るというわけです。
1997年以前、即ち、現行の「JIS B 7420 -1997」(これを「現行JIS」もしくは「新JIS」と呼んでいます)以前の、改訂前のJIS規格(これを「旧規格」と呼んでいます)では、もちろん、「工作用」と「検査用」のそれぞれについてゲージの製作公差が規定されており、当然、メーカー側としては工作用として製作するのか検査用として製作するのかは事前の必須な確認事項であったわけでした。
しかしながら、現行JISでは、ゲージの製作公差は工作用ゲージのみが規定され、検査用ゲージについては規制から外されています。
なぜ規制から外されたかという理由・事情というものは、おそらくは推測の域を出ませんが、1997年の現行JIS規格の改訂に際して、IT5級用ゲージの製作公差の規定も外されたわけでしたが、その理由として「IT5級用ゲージの製作公差を規定しても、実際にはメーカーは製作能力がないだろうから、意味がない」ということのようでしたから、同じ理由でもって「検査用ゲージの製作公差を規定しても、メーカーにはその製作能力がないだろうから、規定する意味がない」という次第であったように思えます。
この新JISの改訂に際して何が改訂されたかといえば、ISOにも準拠するという目的はあったわけでしたが、ゲージの製作公差の点から言えば、例えば、基準寸法18-30mmのハサミゲージで、IT6級を見ると、旧JISではゲージの製作公差幅は2.4μmでしたが、現行JISでは4.0μmに拡張されています。
このゲージの製作公差の寸法許容幅を拡張した分はそのワーク側の加工許容幅を狭めたわけですから、一般にワークの機械加工をするユーザーの負担において、ゲージ・メーカーの製作能力の不全を救済したとも言えるわけです。
しかしながら、IT5級用ゲージの需要は変わらずにあるわけですし検査用ゲージの需要もあるわけで、それに対して十分に対応できるゲージ・メーカーも現にあるわけですから、上述した現行JISを規定した「日本工業標準調査会」の審議での現状認識が正しく妥当なものであったかどうかが問われるわけです。
そういった「批判」はともかく。
IT5級用ゲージの製作要求があった場合、現行JISの規定外ですから、旧JIS規定が引き続き有効性を残続させているという理解、同時に、検査用ゲージの製作要求に関しても同じ考え方で、対応しています。
「日本工業標準調査会」の審議で表面化した、従前の、「IT5級ゲージ」なり「検査用ゲージ」のゲージ製作公差を充足でき得るメーカーはないだろうという割り切りは、その審議に加わっていたゲージ・メーカがハサミゲージに関しては内製していないようですから、ゲージの製作技術・技能が見えなくなっているという実情を反映していたのではないかと思えます。
特に、ハサミゲージの製作技術・技能は、関西で言えば「大阪陸軍造兵敞」での製作技術・技能が公の権威でもって確立されましたから、いわゆる「鋳物製ラップ工具+WA砥粒+ラップ油」という遊離砥粒ラップ/湿式の技法が総てであるかのように後進の育成にも適用されたわけでした。しかしながら、この方法でしかゲージ製作は出来ないかという疑問は、つまり、他の技法の適用の可能性は、その当時でも十分に意識され検討されたはずでしたが、もっとも簡便な方法であり、同時に、ゲージ工の養成が容易であるという事実は、戦時下の社会状況の下では、とにもかくにもその技法に依拠されたわけだったでしょう。
この技法が、戦後に世代継承されて行くにつれて、個々の「改善」とか「独自な工夫」によって、却って遊離砥粒ラップ/湿式の技法の「限界」が露呈してきたわけです。
だから、現役のゲージ職人の技術・技能が承継できないとか、あるいは、特殊なゲージ材質(例えば、SKS2/SKD11/ハイス/超硬)に対してはそのままでは対応できないとか、いろいろな問題を抱え込むことになりました。
ゲージの製作技術・技能は「ハンド・ラップ」という技能に集約されますが、その再構築が必要なわけです。
16. アメス・ポータブル硬度計
現在では、焼き入れの硬度については全量検査を心掛けている。
ゲージ屋ならどこさんでも同じだろうが、いちいち焼き入れ硬度を数値で検証しなくても、この色まで加熱しているからこういう焼き入れができていると分かるわけだから、いちいち測定機を持ち出して検証されるという事例はあまり見掛けたことはない。
私らでも、そういうように教わってきたし、念のためにということで、いろいろと熱処理条件を変えて焼き入れサンプルを作り、専門業者さんの所でロックウェル硬度計で測定させてもらったことがある。
通常なら、罫書き針の先で焼き入れ個所を罫書いてみる、ヤスリで擦ってみる、といった作業で異常は容易に発見できるのだが、正面から数値で管理すべきかどうかという問題に持ち込まれると、実は、扱いに困る。
その「扱いに困った事例」というのが、ISO9001の受審に際してであった。
(ISO9001殿関連での論議は、また別の機会を設けてするようにします。)
問題は、ダイス鋼の焼き入れ。
普通、工具鋼の場合、多少焼き入れ温度が高くなっていても、あるいは低くなっていたとしても、一定の温度幅の範囲内ではきちんとHRc60が保証される(そうなるように設計されている)。だから失敗がないし、あるいは、余程間の抜けたことであった場合以外には、失敗のしようがない。
ところが、ダイス鋼の場合、その最適焼き入れ温度の「幅」というものが余程狭いようで、ちょっと過熱したり、加熱不足であったりすると、てきめんにその焼き入れ硬度が変動してしまう。
焼き入れに失敗したからといって簡単に焼き戻しがすんなり出来るというわけではないので、いろいろと条件を探って、最適手順というものを確定し、かつ、その手順に習熟しないといけない。
そのために、アメス社のポータブル硬度計(ロックウェル)を購入し、硬度測定をしているわけである。
17. ハサミゲージの仕様
右の写真は、ダイス鋼製のハサミゲージで、これから仕上げに入ります。
仕上げについては別に説明しますが、ここでは具体的な使用の問題を論議します。
左側の小さな方は、規格は20js6。
JIS規格形状では、幅65×長さ70ですが、ここでは65×75。
大きな方は、規格が30h6。
JIS規格形状では、幅75×長さ80ですが、ここでは75×85。
つまり、JIS規格形状ではいかにも具合が悪いと判断できる場合には、当方で修正を加えています。
一番の問題は、ゲージ上辺から10mm入ったセンター線上にタグを結びつけられるように5mmφの穴を明け、あるいは、ユーザーが指定する兵数字を刻印する領域を確保するために、仕様形状に手を加えるわけです。
ゲージ厚さは、JIS規格形状のままです。
別段、それで不都合はないはずですが、6Tとか8T、場合によっては10Tを求められることがあります。
なぜかという疑問を持ってきたのですが、あるユーザーの声として、ゲージ面の磨損が看過できないため、厚みを大きくすればその磨損対策になるからということがありました。
ゲージ材質の選択・採用の問題に帰着します。
18. 仕上げ工程とブロックゲージ
ハサミゲージの仕上げ工程は、ブロックゲージとの比較測長で、平面度・平行度・寸法値を追い求めていくわけなのだが、そのブロックゲージの信頼性が劣化していると何の意味もないことになる。
規準になるブロックゲージは、当然なことながら、ブロックゲージ・メーカーに委託して定期的に校正しているわけなのだが、ブロックゲージを使って仕上げをするということは、ブロックゲージがどんどん磨損していくことを意味するから、校正時の寸法精度がどれくらいの期間維持されているのかという問題も併せて問われることになる。
当方では、最終仕上げに至るまでは、つまり仕上げるべき寸法値の1μm手前まで、JIS2級のブロックゲージ・47個セットを使う。もちろん、1.001-1.009の9個セットを併用し、併せて、超硬製保護ブロックゲージ1mmセットを使うことも勿論である。なぜ1μm手前かと言えば、2級ブロックゲージは、プラス・マイナスの両方向での公差が認められているため、ブロックゲージの貼り合わせ個数によっては、公称寸法よりも大きな組み合わせになっている場合があり得る。もっとも、この点は購入当初の場合での問題であって、それ以降は、使用頻度に従って磨損が進行していくから、組み合わせの公称寸法を上回るという心配はなくなる。
このように、ブロックゲージ・セットを分けるということを試みたのは、ダイヤモンド砥粒を使った遊離砥粒ラップ/湿式の技法を採用してハサミゲージを製作していた当時、あまりにもブロックゲージの損耗が激しいからであった。
もちろん、超硬製保護ブロックゲージを両サイドに貼り付けるのだが、20個~30個も仕上げれば、それが2μm程は磨滅するわけで、タチの悪いことには0.5μm粒径砥粒を採用していたから、磨損情況が視認できない。
超硬素材というのは、ダイヤモンド砥粒に対しては耐性が無く、簡単に磨滅していく。
もっとも、ダイヤモンド砥粒の研磨力を最大限に引き出せるように道具立てを考案しているわけだから、ゲージ面を効率よくラップできるということは、ブロックゲージの側も効率よくラップしているということを意味している。
遊離砥粒ラップ/湿式の方式を放棄して固定砥粒ラップ/乾式の方式に移行して以降は、ブロックゲージの磨損は激減したわけで、それでも、3年間の校正周期の期間中で、0.3μm程度の磨損が検知される。従って、このデータに従えば、ブロックゲージの磨損ということが回避できないならば、特定のブロックゲージに磨損が集中するような使用法を考え、同時に、少なくとも1年間を経過する以前には新しいブロックゲージと差し替えるということで、全体としてのブロックゲージ・セットの精度条件は維持されるわけである。
2級ブロックゲージ・セットの活用は、それが最終寸法仕上げの手前の段階だから、例え磨損情況を看過してしまっていたとしても、それは、まだ残りの仕上げ代寸法が予期したものよりも大きかったという結果をもたらすことでしかないから、「寸法を取り過ぎて大きな寸法に仕上がった」という「失敗」に結果するものではない。
もっとも、「1μmの仕上げ代が残されているはずが、2μm残っていた」というと最終仕上げ(鏡面ラップ工程)に難儀するから、この2級ブロックゲージ・セットも、あまり磨損が進行してしまう前に新品と差し替えないといけない。
以上の点が、ISO9001でいう「測定機器の監視」の内容になっている。
19. 仕上げ工程とブロックゲージ(続)
最終仕上げと寸法検証には、JIS1級・103個セットを使用する。
もちろん、0.991~0.999の9個セットも必須ではあり。
貼り合わせ枚数を少なくできるだけ、ブロックゲージの寸法変位の影響を小さくできる。
検査用にはJIS0級ブロックゲージを使わないといけないという向きもあるのだが、0級は「基準用」であって、ゲージの製作に直接使用すれば一挙に摩耗をきたすので、寸法精度が定義できなくなる。
ブロックゲージを検定する検査設備を持つということが考えられるのだが、0.01μmレベルを測定するという作業は、例えゲージ屋であるとしても、あまり現実的な作業ではない。
0級ブロックゲージは、103個セットと47個セットとを持ち合わせている。
ゲージ屋の品質管理システムとしては、0級ブロックゲージを起点として、寸法精度の管理が体系化されるし、また、されないといけないのだが、これは、0.5μm以下のレベルで寸法検証が図られなければならないという業務の特質によるものであって、何でもかんでも0級ブロックゲージでなければならないというものではない。
普通なものづくりでの現場では、マイクロメータでの寸法コントロールが図られれば十分というところでは、2級ブロックゲージを1セット準備しておけば十分なはずだが、どういう話のいきさつか、0級ブロックゲージのセットを売りつけられていた工場があった。そのブロックゲージの寸法検証(校正)のために、デジタル・マイクロメータを使いたいのだが、と言われたときには絶句してしまった。
0級ブロックゲージを規準にして、0.5μmを最小分解能とする比較測長器(コンパレータ)で工作用に使用している2級ブロックゲージの損耗情況を検証するということはもちろん可能で、可能であるばかりか、不断に検証しないと具合の悪い羽目に陥る。
ハサミゲージの作り方としては、どういう特定の寸法値に仕立て上げるかがまず決定されて、その寸法を実現する。
こういう製作姿勢だと、複数個の同一規格のハサミゲージについてそれぞれ同一寸法に仕立てられる。
複数個のゲージが発注されるという場合、その数だけの製造ラインで使用されるということなのだが、例えば、AラインのZ1ゲージで合格したワークが、BラインのZ2ゲージでは不合格となる場合があり得る。特に、ゲージの製作公差範囲が以前より拡がっている現行規格の下では、この心配はいっそう大きい。
従って、ゲージ製作に際しては、軸用の外径用ハサミゲージについては、ゲージの製作公差の最小値で、全数を同一の寸法値にまとめないといけないわけである。
20. 刻印打刻
規格表示その他は刻印で打刻しています。
刻字深さは大体0.1~0.15mmになります。
刻印の大きさは各種ありますから、全体としてバランスのよい表示が出来ます。
21. ダイス鋼製ゲージの仕上がり
ゲージ本体は、#600の研磨布で磨いています。
クロム鋼全般について言えるようですが、例えば、平面研削盤で平面研磨した場合、おおよそ1000℃程度の研削熱に表面が晒されてワーク表面に強制的に酸化クロム層が形成されるようで、その酸化クロム層によって耐錆能力が実現されるということのようですが、ハサミゲージの場合、平面研削による砥石の研削痕というのは「焼き入れ状態」なわけですから、全部表面を除却しないとその後の寸法変位が生じる原因となる。そのために、この研削痕を除却するわけですが、この場合に、併せて表面の酸化クロム層も除却されてしまう。従って、表面を出来るだけ微細・平滑に磨いて、新たに酸化クロム層を生成させなければいけない。
そういう考慮に基づいています。
望むらくは、#800なり#1000の研磨布で磨くといっそう望ましいということになりますが、耐錆性能という点に限れば、#600でほぼ問題の予防にはなります。
寸法実測値を記載した「タグ」を個別に付けます。
仕上がり面は、#8000でのラップ。
固定砥粒ラップ/乾式の場合、#6000ないし#20000のラップで、現品で仕上がり具合を「比較」すればその違いは明晰ですが、そうでなければ、具体的にどの粒度でラップしているかの判別は困難です。つまり、#6000で#20000相当の面粗度を出すとか、#20000で#8000程度の面粗度になってしまうとか、なかなか一筋縄ではいきません。
例えば、特定の寸法ジャストに仕上げるとか、複数個のゲージを総て同じ寸法に仕上げるとかが「ありえないこと」という「常識」があります。そうではなくて、簡単に可能なのだ、むしろ、そうでなければユーザーの方が困ることになるだろうというのが私の主張ではありますが、それが言えるのは、従前よりの「遊離砥粒ラップ/湿式」の方式での「限界」を明らかにできたためです。
遊離砥粒ラップ/湿式という技法は、ワーク面とラップ工具面との間にラップ油の油膜とそれに混ぜ込まれているラップ砥粒が「層」となっているもので、ラップ工具の運用は、ワーク表面に対しては「間接的なもの」になります。
まったく同じ動作でラップ作業を行った場合でも、砥粒の「濃度」、砥粒の「磨損・破砕の情況」等の条件次第によって、その研磨力は大きく変わります。
従って、ワークの寸法を、例えば1μm摺り下ろせたと判断しても、実際に1μm摺り下ろせたか否かは、ブロックゲージで寸法測定してみないと分からない。
つまり、まったく「手探り」になってしまいます。
これに対して、固定砥粒ラップ/乾式の場合、ワーク表面に対するラップ工具の働きは「直接的」ですから、余計な挿雑物がないだけ、作業の目論見を正確に反映することが出来ます。
もっとも、理屈を立てれば、固定砥粒ラップのラップ工具表面においても、ラップ滓の付着や砥粒の「へたり」によって、なかなか思うようにはコントロールが出来ないだろうという指摘にはなるのですが、遊離砥粒ラップ/湿式では非常に困難を極める作業が、それよりも遙かに簡明な手順となりコントロールも容易になるとお答えしないといけないでしょう。
22. 総焼き入れゲージの問題
右の写真のようになったから、これと同じゲージを製作してくれという依頼があった。
当該品は総焼き入れゲージ。
通常は、測定部だけを焼き入れるのだが、何時の頃からか、かなり以前からの話になるのだが、ゲージ全体を焼き入れしろという話が持ち上がってきていた。
なぜ総焼き入れでないといけないかという(ユーザー側からの)理由は、測定部だけの焼き入れ品だと、「寸法がよく狂うから」。
つまり、工具用鋼材(SK5/Sk4/Sk3/SKS3)では、ナマ材のままでは材料強度に不安があるということらしい。
このことが意味していることは、一旦仕上げられたゲージも、「経年変化」で寸法は狂っていくもので、そのことについてはゲージ屋の責任ではなく、材料それ自体の持つ特性の故である、という、ゲージ屋の「不手際」を免責してくれるという話なのである。
総焼き入れゲージとなれば、手間は掛かるし、いろいろと難しい問題が持ち上がるから、その分はコスト高となって高価格になってもやむを得ないという、ゲージ屋にとっては非常に有り難い話ではある。
「経年変化」という言葉が何を意味するかという点が、実は深くは追究されてはいない。
ゲージ製作工程で、無茶な力が加われば、その力が「残留応力」となって寸法の狂いの原因となる。
あるいは、焼き入れに際して「焼き戻し」をしていなければ、そのことが寸法の狂いの原因となる。
これらの問題をきちんと解決して(これは、ゲージ・メーカーの責任だろう)、
それでもゲージの狂いが生じるかどうかが検証されるべきなのである。
板ゲージ用の工具鋼、特に日立金属(株)のYG4/YCS3/SGTは、製鋼段階で「球状化焼き鈍し」がなされていて、工具鋼としての信頼性は絶対的なものであったし、材料としての「強度」も何ら不安を与えるようなものではないわけで、従って、残留応力が蓄積・累積しない加工法でゲージ製作をする、焼き入れに際してはきちんと「焼き戻し」をするということで、問題は生じないように出来るわけなのである。
例えば、材料に強度をもたせようとする場合、ナマ材か、あるいは総焼き入れか、という「二者択一」の発想に安易にとらわれるのだが、鉄鋼材料というものは、ナマ材から総焼き入れに至るまでの間の「中間段階」があるだろうと言えるわけで、その「中間段階」で、必要とされる、あるいは、期待される強度というものを考えるわけである。
なぜならば、総焼き入れゲージとしてしまった場合、ほとんど修正がきかない。
敢えて修正を加えようとすると、かなり無茶な力を加えなければならなくなる。
ゲージとしての信頼性が著しく損なわれるわけである。
だから、私としては、この「中間段階」でゲージ製作をしてきているわけで、だから問題を生じたということはない。
総焼き入れを施せば、寸法とか形状とかがもう変化しないと考える根拠はない。
その材料が持つ「結晶構造」と「残留応力」とはまったく別な次元にあるものだから、総焼き入れしたものも、その製作過程での加工履歴に従って、変化・変位は生じる。
写真の総焼き入れゲージの場合、「曲がり」が出ているわけで、おそらくは、寸法精度に対する信頼性は既に無かったろうと考えられる。また、写真のゲージは、「割れ」を生じているのだが、これは、何もユーザーが現場で無茶な使い方をしたとかというのが原因ではなくて、残留応力の故なのである。
この亀裂部分に残留応力が蓄積されていて、経年に従って、亀裂になって表面化したわけである。
焼き入れがまずかったというわけでもない。
しょっちゅうあることかと問われれば、そうしょっちゅうあるわけではないと答えるわけだが、ただ、珍しい話ではない。
以上の点は、顧客に対して縷々説明もするのだが、顧客側の要求レベルが高いと、ゲージ屋もそれに十分応答するだろうという「期待」があるのかも知れない。
しかしながら、何でもかんでも「経年変化」として、言わば「神のみが知る事態」としてゲージ屋が免責されるのであれば、ゲージ屋の側としては、何も苦労することもないということになる。
ダイス鋼を採用すれば、総焼き入れでないといけないとかどうかの問題は、まったく意味を失う。